Cuttings
Cuttings treatment unit
Eliminating the need for drilling waste to be transported to shore or re-injected.
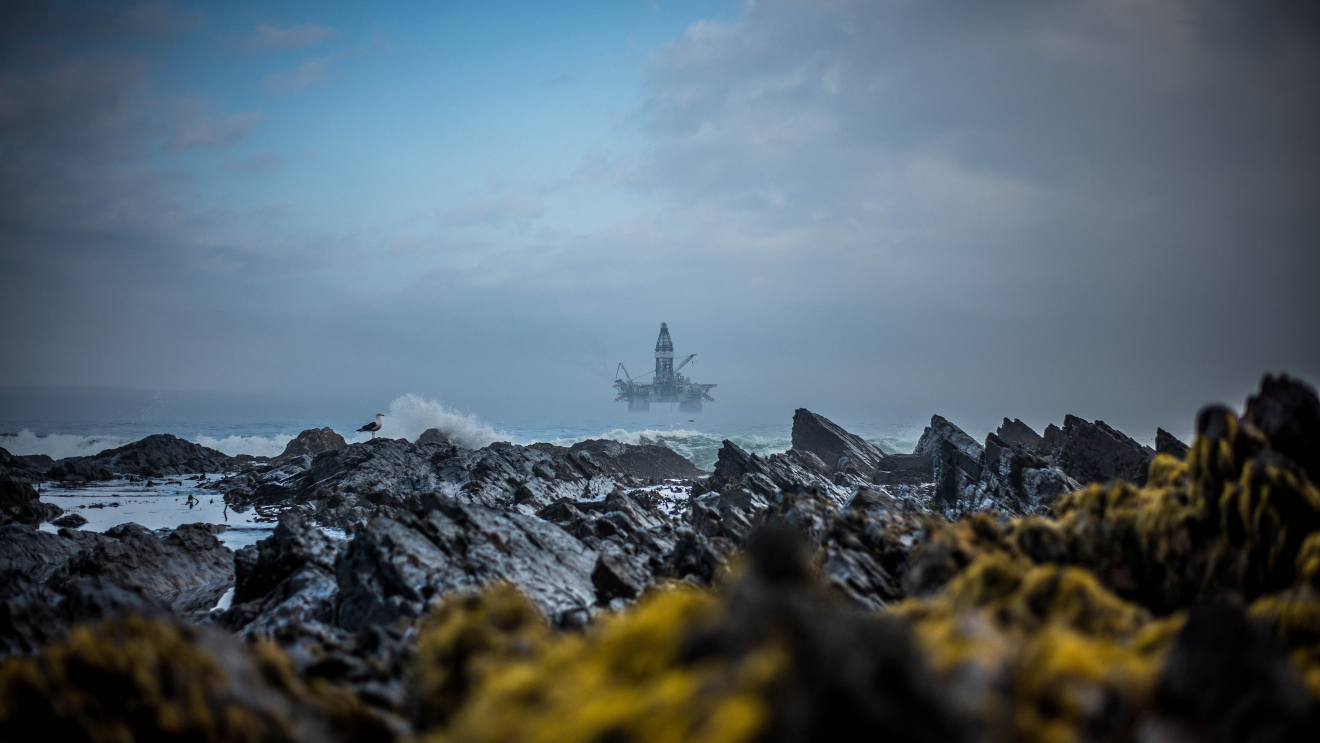
Cuttings treatment unit
Innovation:
Norwegian Technology AS has been awarded a patent on its innovative technology that can efficiently treat drill cuttings offshore on-site at drilling rigs or at fixed installations for safe discharge of solids to sea bed with no environmental impact.
Cost savings:
As an example, this technology can; if implemented on ONE fixed installation save the operator more than 150 million USD pr. year.
Environmental advantages
- Eliminating transport “skip and ship” to shore by ship and truck
- Free up more space on the rigs and installation
- The treated cuttings can be safely placed on the seabed
- Increase the efficiency of the drilling rig
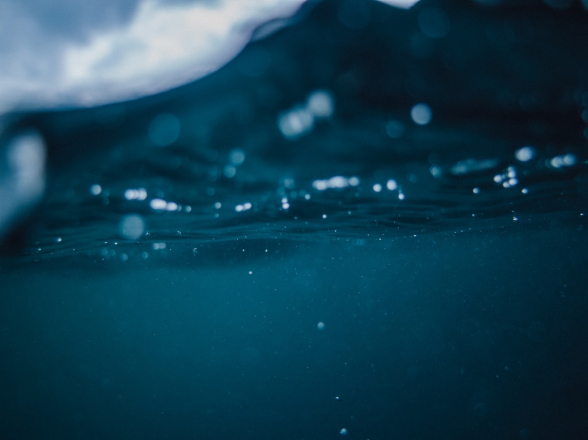
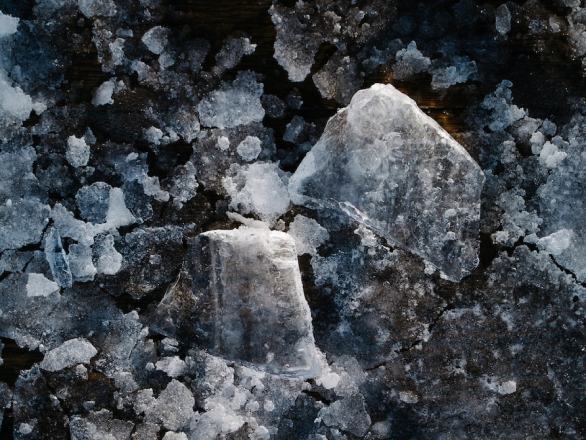

Technical advantages
Foot Print:
Reduced energy consumption will reduce the handling cost, and especially the investment cost. Reducing input power used per ton treated waste will in addition reduce the footprint and weight.
Minimal Noise emission:
The friction heat systems generate high level noise emissions for the operator and the surrounding environment. In comparison, our technology generates minimal noise emission.
No Contact:
There are no moving parts, except a belt or screw conveyor that transports the cuttings trough the separation chamber. No contact and no moving parts contribute to robustness.
Fast startup:
Starting up the heat generator with microwaves is instant. Generating heat from friction requires time.
Robust:
The technology used for heating is known to be very robust. Industries have case references of 20 years of running with no downtime or breakage. Many industries run microwave ovens 24 hours a day, 7 days a week in drying processes, with no downtime over periods of years.
Not crushing particles:
Treating drill cuttings (clay) in a microwave allow for aggregation of small clay particles in to larger porous clay structures. As a result, the solid discharge will sink and can be placed at the planned discharge sight.
Low cost of operation:
Minimal downtime and high component durability combined with low energy consumption makes our technology cost efficient.
Project status
The onshore pilot has been successful and we are now having productive discussions with companies that are eager to start using the system.
Stay tuned!