Baker Hughes
Baker Hughes
Norwegian Technology agreed with Baker Hughes Inc to treat 330 m3 of low solid OBM that had been stored in tanks for several months.
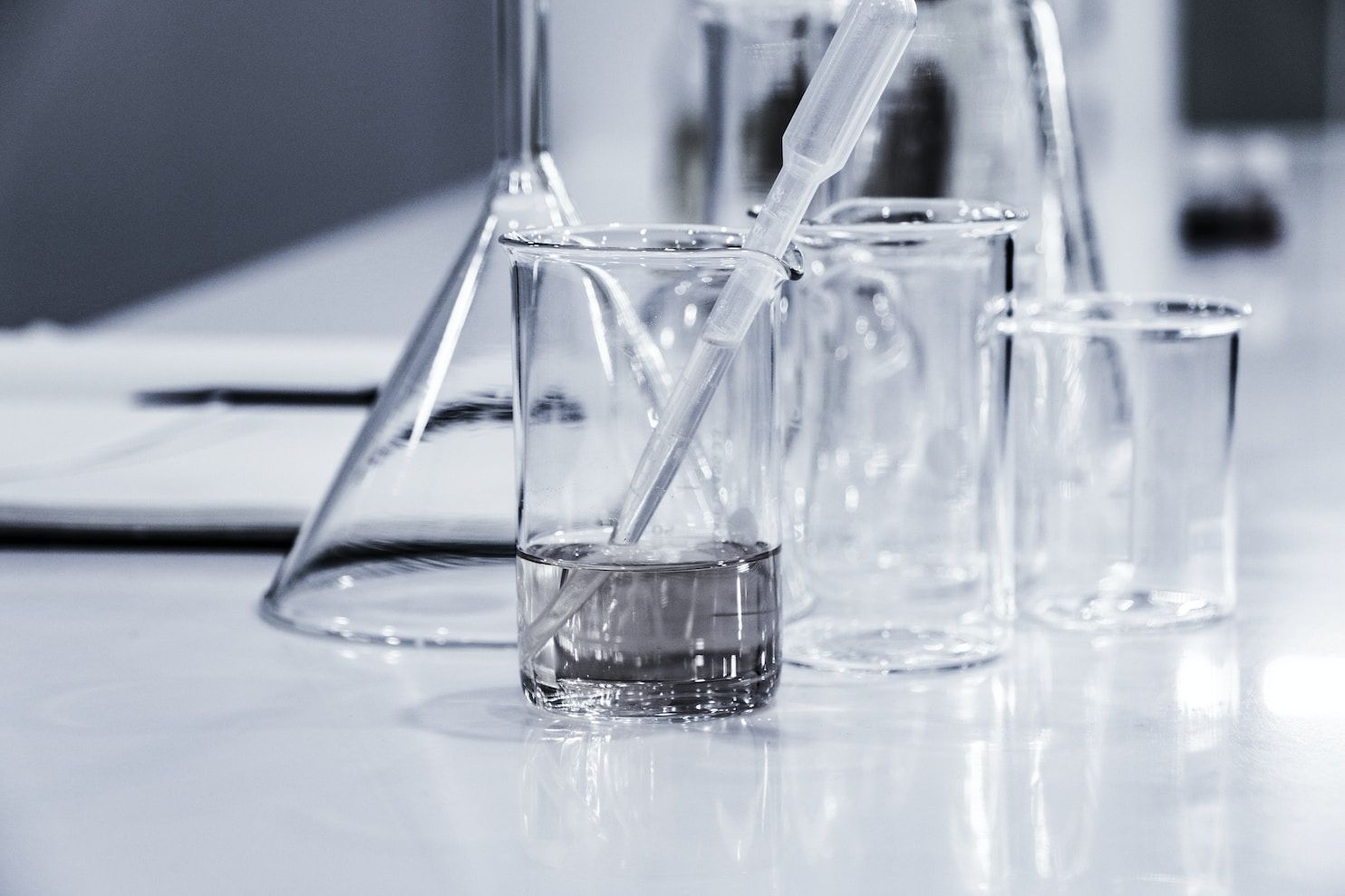
Description
Destabilization and separation of Oil-based drilling fluids
Year
2020 -
Technology
MUD-Split
The recovery for re-use of valuable elements from oil-based fluids contributes to environmental stewardship, circular economy, and optimal waste treatment.
In Norway, approximately 180,000 ton of high-priced oil-based mud and completion fluids return to shore after having been used offshore. The used oil-based mud, actually a valuable resource, could be treated, upgraded and reused. Very often, instead, the treatment is not carried out because the used oil-based mud (OBM), even after the upgrading, is deemed unsuitable for the stringent requirements of the drilling operations. A substantial amount of OBM is therefore classified as waste.
The OBM waste handling costs around USD $300 per ton, the figure is based on data received from Norsk Gjenvinning AS. Furthermore, some used oil-based drilling and completion fluids are stored in tanks for several years as they contain highly expensive chemicals.
Norwegian Technology AS agreed with Baker Hughes Inc to treat 330 m3 of low solid OBM that had been stored in tanks for several months. The mud contained 60% of expensive brine and around 40% of oil (by volume). The mud was treated and approximately 60% brine, 20% oil and 20% sludge were recovered.
Challenge
The price of the OBM is a function of its composition, illustrated in the figure below (IPIECA/OGP, 2009). The quantities of the various components can vary significantly, e.g. the oil/brine ratio can range between 60/40 and 90/10 (McCosh, Kapila, Dixit, Way & Phipps, 2009), while the weighting material can sometimes be close to zero.
Low oil prices, difficult drilling settings and stricter environmental regulations promote the development of new practices in the oil and gas industry. The optimization of the waste treatment can contribute to significant cost savings. OBM is an expensive drilling fluid which is necessary in many drilling operations. The price of materials used in the OBM can range from USD $ 250 to 2 500 per m3 (Melton et al., 2004).
Chemically separated
The drilling mud is chemically separated into four fractions (Oil, sludge, brine and solids). The type of chemicals and quantities utilized to destabilize the mud vary and depend on the mud characteristics. For this project, the best chemical compound for the destabilization of the low solid OBM was the Mudsplit 001 with a dosing in the range of 3-4 l/m3. The Mudsplit 001 is one of the chemicals supplied by Norwegian Technology for the destabilization of the OBM.
The solid fraction was not quantified during the separation as the amount was not detected visually. Both the brine and the oil fraction were clear and transparent after destabilization and separation. The two diagrams present the volumetric fraction of each component.
The two graphs below also illustrate the efficiency of the MUD Split 001. It is important that in a retort analysis (evaporation), the dissolved ions in the brine fraction remain in the sample and therefore contribute to the solid fraction. As a result, the chemically separated mud contains more brine than water.
“330 m3 of OBM with a density of 1.76 ton per m3, 581 metric ton, were treated resulting in an extremely positive Commercial Case.”
References
Den Norske Veritas. (2013). Rapport Vurdering av oljeholdig avfall fra petroleumsvirksomheten til havs. DNV referanse:nr. 149JIOC-3, Rapport:nr. 2012-4087/DNV.
IPIECA/OGP. (2009). Drilling fluids and health risk management. London, UK: International Petroleum Industry Environmental Conservation Association, International Association of Oil & Gas Producers.
McCosh, K. L., Kapila, M., Dixit, R., Way, P. W., & Phipps, J. (2009). Continuous Improvement in Slop-Mud Treatment Technology. SPE Drilling & Completion, 24(03), 418-423.
Melton, H., Smith, J., Mairs, H., Bernier, R., Garland, E., Glickman, A., . . . Campbell, J. (2004). Environmental aspects of the use and disposal of non aqueous drilling fluids associated with offshore oil & gas operations. Paper presented at the SPE International Conference on Health, Safety, and Environment in Oil and Gas Exploration and Production.
Svensen, T., & Taugbol, K. (2011). Drilling Waste Handling in Challenging Offshore Operations (Russian). Paper presented at the SPE Arctic and Extreme Environments Conference and Exhibition.